aktuelle
Projekte
Umformende Fügeprozesse, wie zum Beispiel das Clinchen, sind in der Automobilindustrie und im Maschinenbau essentiell für die effiziente Fertigung von Mischbaustrukturen. Bei bestimmten Werkstoffen ist eine Erwärmung vor dem Umformen vorteilhaft. Die Additive Fertigung (AM) von Hochleistungskeramiken (HLK) und Multimaterialbauteilen ermöglicht direkt temperierbare Fügewerkzeuge aus HLK. Diese Werkzeuge erzeugen effizient Wärme und können Temperaturmessstellen enthalten. Dies ermöglicht die direkte Überwachung und Regelung der Temperatur. Die CerAM MMJ-Technologie des IKTS, speziell für AM von Multimaterialbauteilen entwickelt, bildet die Grundlage für die AMAREA Technology GmbH (2023). Das Vorhaben zielt auf die Realisierung und Validierung funktionalisierter Fügewerkzeuge aus HLK durch reale Fügeversuche am IWU, um das Potenzial dieser Entwicklungen am Beispiel des umformenden Fügeverfahrens Clinchen zu demonstrieren.
Die WEAM-Technologie des Fraunhofer IWU ermöglicht die vollautomatische Verbindung von Drahtkomponenten mit verschiedenen Substraten. Standarddrähte oder -litzen werden dabei von einem Polymer ummantelt, das elektrische Isolation bietet und die Verbindung zum Substrat herstellt. Diese Technologie ermöglicht die Herstellung von intelligenten, hochintegrierten Bauteilen mit Anwendungen in der Leistungselektronik, Sensorik und Aktorik. Der aktuelle Stand befindet sich auf TRL 6. Mit Unterstützung des Leistungszentrums soll die Technologie auf TRL 7 gebracht werden, indem ein Prototyp im operativen Umfeld demonstriert und auf Dauerfestigkeit getestet wird. Zur Evaluierung des Businessmodells und Analyse von Weiterentwicklungsoptionen soll der Deutsche Technologiedienst (DTD) beauftragt werden. Parallel dazu wird am IWU ein Businessplan erarbeitet. Damit soll die Basis für eine Ausgründung geschaffen werden, welche WEAM zur Marktreife bringt und kommerziell verfügbar macht.
Wieder einmal packt Fraunhofer die Probleme der Industrie direkt an der Wurzel. „Industrie 4.0“ und „Machine Learning“ bieten große Potenziale, benötigen dafür jedoch die passenden Daten. Dabei wird häufig vernachlässigt, dass die Datenbeschaffung und -lagerung, sowie die Modellbildung nicht dem Selbstzweck dienen, sondern zu konkreten Kosteneinsparungen führen müssen. Mit MetaMess substituieren wir teure, absolutgenaue optische Messanlagen durch preisgünstige Linienlaser, speichern hunderte Megabyte große Messprojekte in wenigen Kilobyte großen Kompressionsarrays und pressen den Messprozess in Transfer- oder Handlingoperationen.
Wir freuen uns auf die Gelegenheit, ab dem kommenden Herbst Interessierten aus den Bereichen der Messtechnik, der Blechverarbeitung, der Kunststoffindustrie und Weiteren unser Verfahren live am IWU Standort in Dresden zu präsentieren. Angestrebt wird zudem, dass das Verfahren neben unserem Use-Case an der IWU-Benchmarkbaugruppe - nach geringer Anpassung - auch an Partnerbauteilen verifiziert werden kann.
Mit dem patentierten In-vitro-Testsystem „ClicKit-Well“ steht ein seriennahes Prüfverfahren für standardisierte, quantifizierbare Materialtests kurz vor dem Markteintritt. Ursprünglich für Biokompatibilitätsstudien entwickelt, eröffnet sich im Mikrobiologie-Markt ein zusätzliches, vielversprechendes Anwendungsfeld – insbesondere bei der Bewertung antimikrobieller Oberflächen, die seit COVID-19 stark an Relevanz gewonnen haben. Ziel von TRACe-M ist es, das „ClicKit-Well“ als neues Standardtestsystem in der Mikrobiologie zu etablieren, die bestehende Lücken in der quantitativen Vergleichbarkeit unterschiedlicher Materialien zu schließen und so die Grundlage für eine breite industrielle Nutzung zu schaffen. Nutzen Sie die Gelegenheit, sich frühzeitig als Partner, Anwender oder Lizenznehmer einzubringen. Ein kurzes Video vermittelt Ihnen einen ersten Eindruck von Funktion und Anwendung des Systems: https://www.youtube.com/watch?v=M3KKgVONlBg. Gerne informieren wir Sie über Kooperationsmöglichkeiten und nächste Schritte.
Im Vorhaben "PCR-Chip Demonstrator" wollen wir einen niederschwelligen Zugang zur molekularen Diagnostik ermöglichen. Molekulare Diagnostik, d.h. die Detektion von spezifischen DNA-Molekülen, erlaubt unter anderem den schnellen Vorort-Test auf Krankheitserreger. Hierfür werden wir einen existierenden PCR-Chip, der den grundlegenden Prozess der DNA-Vervielfältigung in einem miniaturisierten Format realisiert, zu einem Entwicklungs-Kit weiterentwickeln. Dieses soll zum einen die Leistungsfähigkeit des Chips demonstrieren, aber vor allem zu eigenen Experimenten mit der Technologie befähigen. Gemeinsam mit potenziellen Kunden wollen wir konkrete, analytische Fragestellungen auf die Chipplattform übertragen und so gemeinsam neue Anwendungen erschließen. Der PCR-Chip Demonstrator wir u.a. zum Chemnitzer Seminar „One Health“ (3./4.09.25) und auf dem ENAS-Messestand zur Compamed (17.-19.11.25) live zu erleben sein.
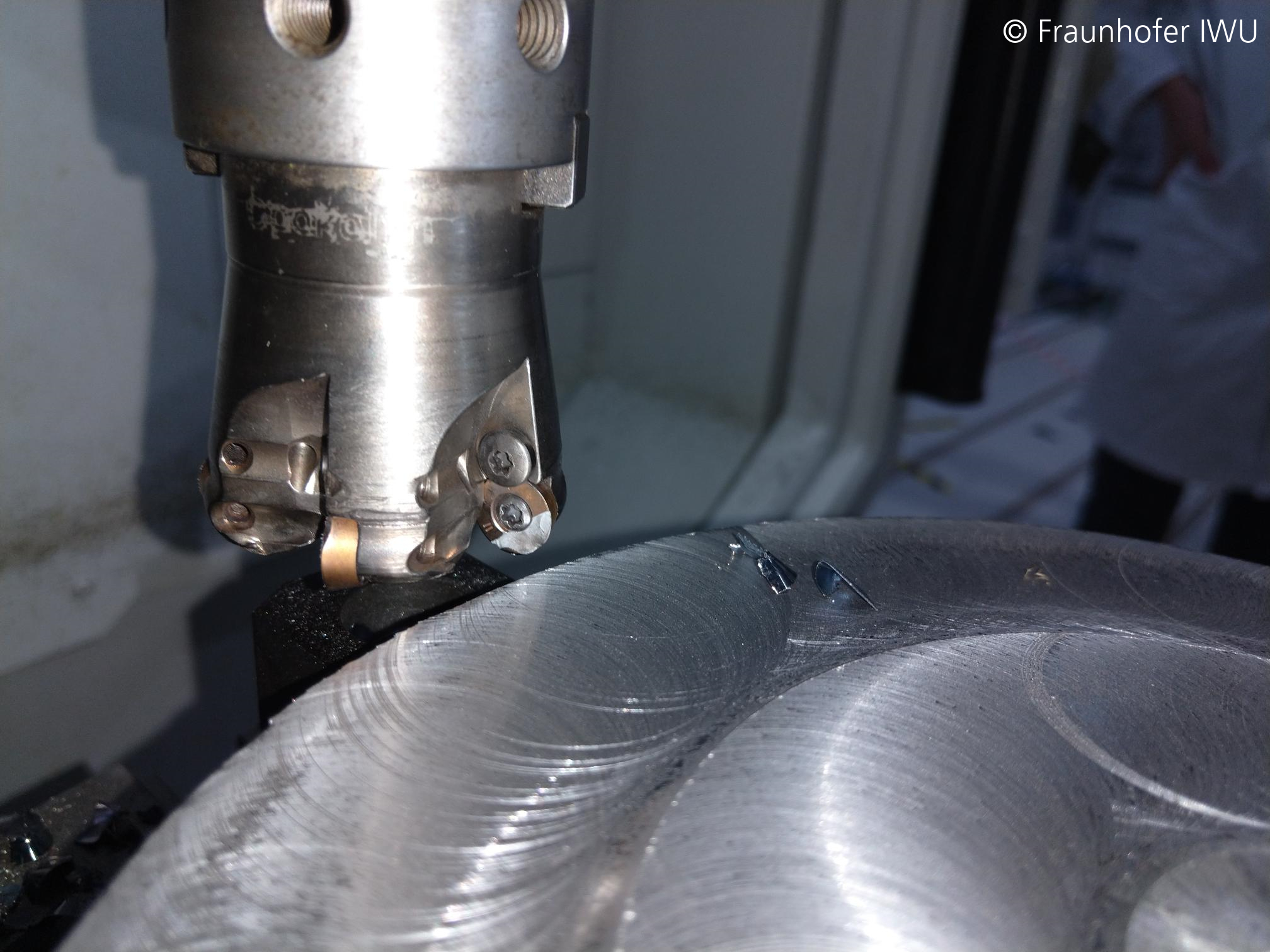
Bohren, Fräsen und andere Zerspanprozesse gehören nach wie vor zu den wichtigsten Verfahren in der industriellen Fertigung. Für eine moderne und effiziente Fertigung ist es notwendig, Werkzeugbruch bzw. den Bruch einzelner Werkzeugschneiden im Prozess zuverlässig und automatisiert zu erkennen. Existierende Systeme sind jedoch kosten- bzw. wartungsintensiv, produzieren häufig Fehlalarme oder können einen Bruch erst nach dem eigentlichen Zerspanprozess detektieren.
Am Fraunhofer IWU wurde ein innovativer Algorithmus entwickelt, welcher adaptiv, d.h. ohne spezielle Trainingsdaten oder Referenzkurven, auf Basis existierender maschineninterner Daten zuverlässig Werkzeug- sowie Schneidenbruch erkennen kann. Ziel des Projektes ist es, den an Offline-Daten erprobten Algorithmus an einer Maschine im Versuchsfeld zu implementieren, so dass das System zur Schneidenbrucherkennung online erprobt und demonstriert werden kann.
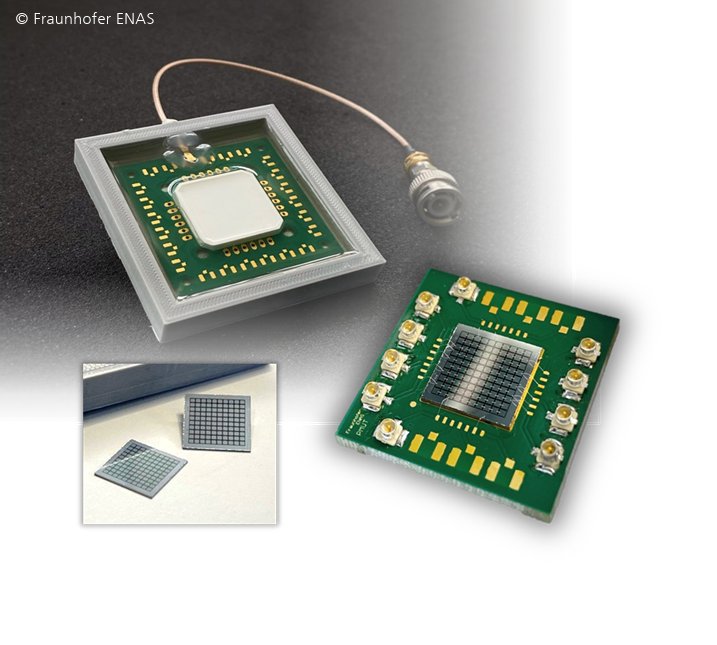
Ultraschalltechnologie ist in vielen Bereichen unverzichtbar – von der zerstörungsfreien Bauteilprüfung über medizinische Bildgebung bis hin zur Gestenerkennung im Automobilbereich. Unser Ziel ist die Bereitstellung leistungsfähiger, kostengünstiger und vielseitig einsetzbarer Ultraschallwandler auf Basis der PMUT-Technologie (Piezoelectric Micromachined Ultrasonic Transducer).
Unsere Aluminiumnitrid-basierten PMUTs zeichnen sich durch eine hohe Effizienz, Langlebigkeit und flexible Anpassung an verschiedene Anwendungen aus. Durch ihr hohes Miniaturisierungspotential und die Möglichkeit zur Serienfertigung bieten sie eine wirtschaftliche Alternative zu konventionellen Ultraschallwandlern.
Im Projekt des Fraunhofer ENAS werden gehauste PMUT-Evaluierungsmuster entwickelt, die potenzielle Anwender in ihrer spezifischen Anwendung testen können. Damit wird der Einstieg in die Technologie erleichtert und neue Möglichkeiten für Industrie und IoT eröffnet.
Weitere Informationen zu unseren PMUT-Varianten und deren Eigenschaften finden sich im Whitepaper.
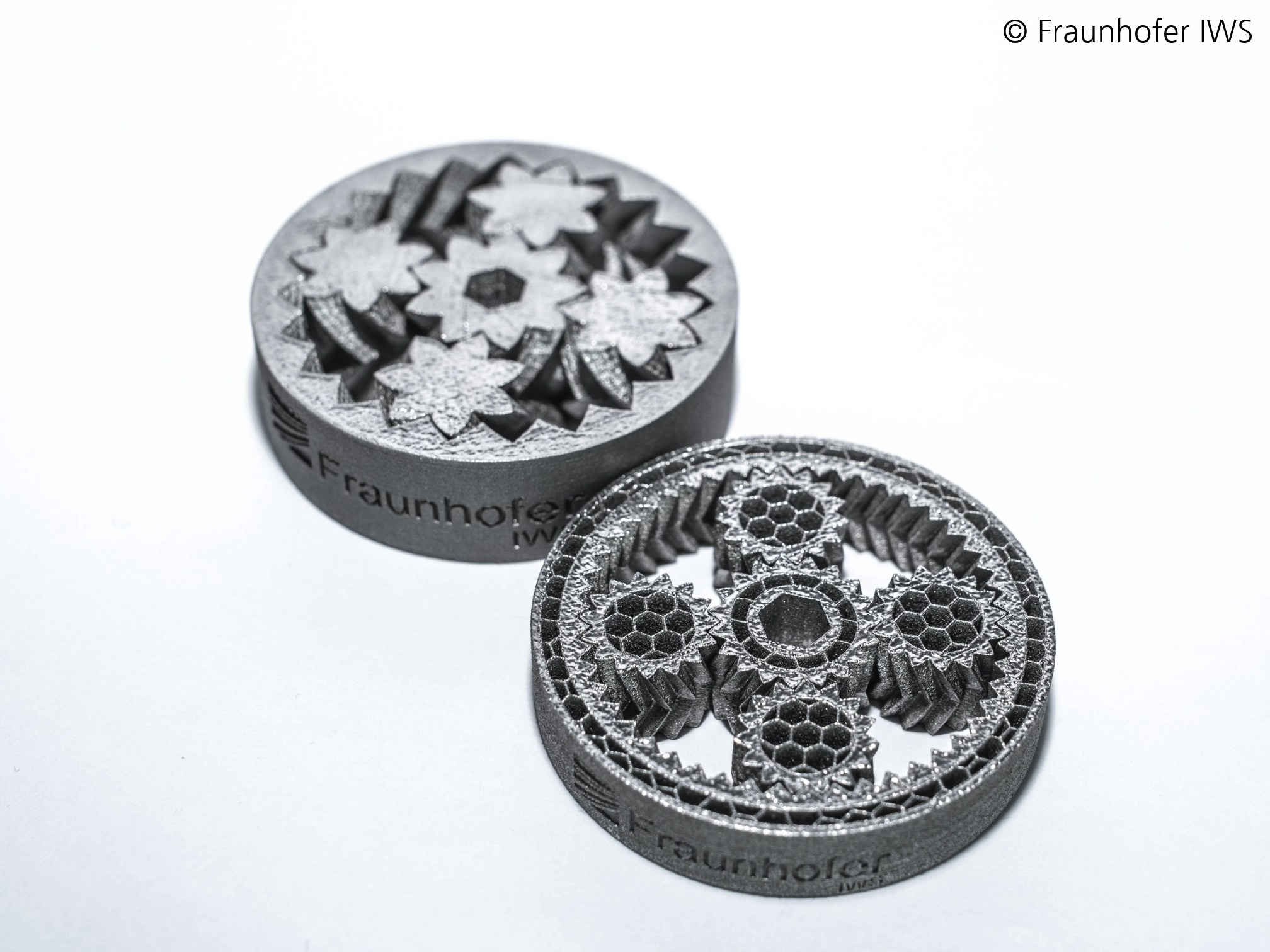
Additive Fertigung: Ist Ihr Teil machbar?
Das Leistungszentrum bietet ein breites Portfolio moderner Produktionstechnologien – darunter die additive Fertigung (AM) oder hybride Verfahren. Dank der Designfreiheit ermöglicht AM die Herstellung innovativer, hochfunktionaler und zuverlässiger Komponenten. Besonders Branchen wie die Luft- und Raumfahrt sowie die Medizintechnik profitieren hiervon. Doch für kleine/mittlere Unternehmen sind die hohen Investitionskosten und der Einarbeitungsaufwand oft eine Hürde. Um den Einstieg zu erleichtern, startet das Leistungszentrum einen Innovationswettbewerb für Prototypen sächsischer Unternehmen:
Sie erhalten eine Machbarkeitsbewertung und der anspruchsvollste, herstellbare Prototyp (Materialwert bis zu 2.000 €) wird kostenfrei gefertigt und auf Fachmessen präsentiert. Nehmen Sie jetzt teil!
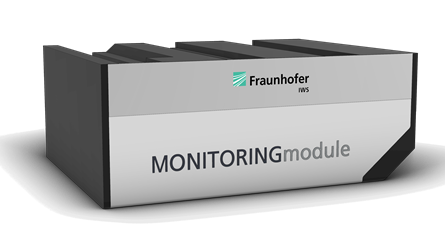
Die Oberflächenstrukturierung mittels gepulster Laser ermöglicht die gezielte Funktionalisierung von Materialien, ohne zusätzliche Beschichtung. Die erzeugten Mikrostrukturen behalten die mechanischen Eigenschaften des Grundmaterials bei, während zusätzliche Prozessschritte entfallen. Entscheidend für die Qualität ist die stabile Prozesssteuerung, da Parameterschwankungen diese beeinflussen und die Funktionalisierung beeinträchtigen können. In zwei öffentlich geförderten Projekten hat das Fraunhofer IWS Monitoring-Ansätze entwickelt, die auf der Analyse akustischer Prozessemissionen basieren. Diese ermöglichen die Früherkennung von Schwankungen während der Mikrostrukturierung und deren Ausgleich in Echtzeit. Das Vorhaben zielt auf die Integration dieser Technologie in eine kompakte, modulare Monitoring-Einheit, die in bestehende Laseranlagen integriert werden kann.
Die Partner des Leistungszentrums SPM haben ein umfassendes Schulungsangebot entwickelt, das den Forschungstransfer unterstützt. Im Einklang mit den Zielen der Fraunhofer-Gesellschaft werden Forschungsergebnisse für die Industrie aufbereitet. Diese Schulungen tragen bereits wesentlich zu den Industrieerträgen der beteiligten Institute bei.
Trotz verschiedener Marketingmaßnahmen wie Direct Mail und Kaltakquise waren die Buchungszahlen für die Schulungen bislang unterschiedlich. Recherchen zeigen ungenutzte Zielgruppen und Umsatzpotenziale. Das Kooperationsprojekt zielt darauf ab, die Akquisition im Bereich Weiterbildung und Wissenstransfer zu bündeln und zu optimieren.
Durch gezielte Marktansprache, insbesondere die Nutzung von Weiterbildungsplattformen, soll die Sichtbarkeit des Schulungsangebots für Industriekunden erhöht werden. Dies fördert den Wissens- und Technologietransfer sowie die Akquise neuer Partner und Projekte.